Cast-3DPrint
Software FOR 3D METAL PRINT SIMULATION
Cast-3DPrint is a powerful design & simulation environment for "get it right" optimization of power bed additive manufacturing processes for metal.
Cast-3DPrint allows accurate prediction of the distortion and residual stresses in the printed part, then provides the guidance to part design and manufacturing process modification to ensure the 'time to market' and 'quality to market'.

3D printing simulations help to understand and visualize the complex thermo-mechanical phenomena taking place during manufacturing, resulting in the production of high-quality, high-accuracy parts.
The Simulation helps evaluate the mechanical performance of a part under certain conditions related to its function, while the former helps predict the result of the 3D printing process, layer-by-layer and under certain process parameters.
Why Use Simulations?
- Avoid print failures and parts rejected for geometric issues, saving time and reducing overall cost.
- Evaluate the risk of production and give pointers to mitigate the probability of failure.
- Understand the physics of the manufacturing process.
- Predict the microstructural characteristics of the end part.
- Optimize production to improve manufacturing speed, reduce post-processing operations or improve accuracy by reducing the part and support deformation.
- Before support generation, simulation results help identify critical areas of significant deformation or internal stress during manufacturing. The designer can then add adapted support structures to minimize the deformation, change the print orientation to change the areas of heat accumulation or modify the geometry of the 3D model to improve the quality of the end result.
- After support generation, simulations help minimize the risk of production failure, ensure that the dimensions of the final part lie within a specified tolerance range and evaluate the impact of different print parameters.
Simulation Result
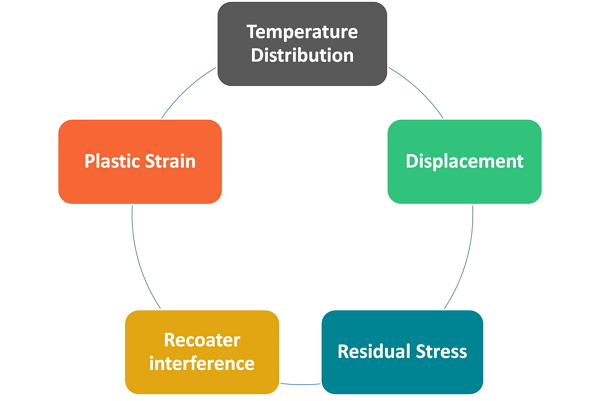
Different part orientation and support
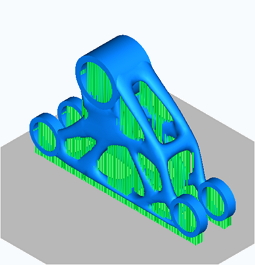
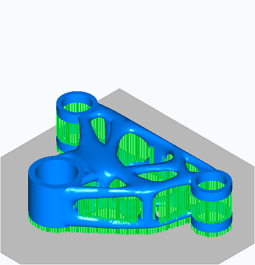
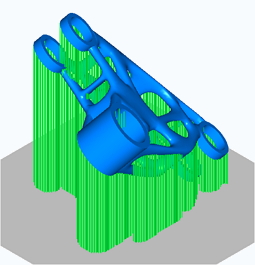
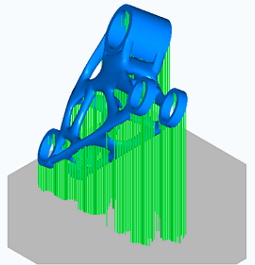
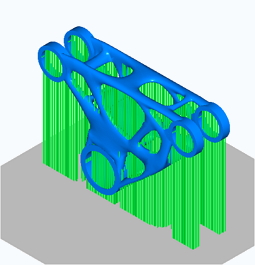

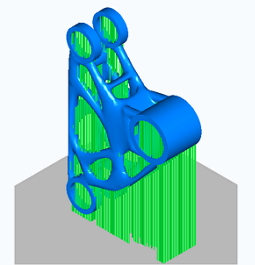
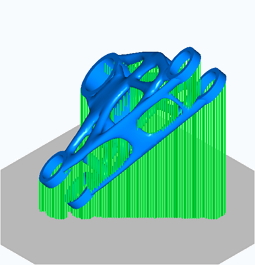
Simulation Step
The first step of a good simulation is the correct discretization of the part volume. Unlike regular mechanical simulation, which uses conformal meshing with tetrahedrons, the 3D printing simulation use voxelization. the 3D volume of the part is represented by small cubes.
Cast-3DPrint can predict part shape, distortion and stresses before printing. It facilitates the set up and solving of print simulations, while offering maximum flexibility for adjusting workflow settings as needed.
- Generate efficient lattice structures
- Simulate the thermal-mechanical build process for accurate prediction of part distortion and stresses
- Use of nonlinear and temperature-dependent material properties (with no inherent strain assumptions)
- Efficient HPC performance scaling
3D Printing Processes
Simulations are most relevant for high-value and high-precision 3D printing. Moreover, the most popular contemporary 3D printing simulation packages are based on metal welding simulation solvers. Thus simulations are more commonly used with metal 3D printing.
However, all main 3D printing processes can be simulated.
Manufacturing Processes Addressed with Cast-3DPrint
- Selective Laser Sintering (SLS)
- Selective Laser Melting (SLM)
- Direct Metal Laser Sintering (DMLS)
- Electron Beam Melting (EBM)
Pre-Deformation
Although it's possible to solve manufacturing problem by finding the best orientation, having optimal support structures and a nice design for AM, distortion issues cannot always be avoided. Even heat-treatment cannot reduce the contraction that occurs during the process.
To avoid high deviation on large or think structures, the method of ‘pre-deformation’ can be applied. Based on the simulated displacements, the geometry is modified in a way, that contraction during the process leads to an accurate part. This step then becomes an additional part of the digital job preparation workflow.
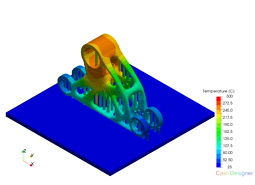
Temperature distribution
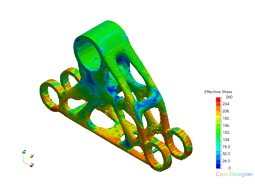
Effective stress
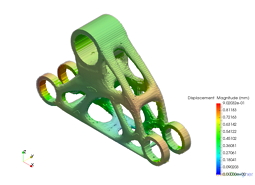
Displacement after print
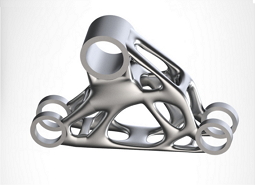
Real printed part after surface finish
SOFTWARE ENVIRONMENT
Cast-3DPrint comes with a best-in-class GUI ensuring an extraordinary user experience:
- User-friendly, intuitive use
- Prepared for application and machine specific dialogs
- Support of complex models
- GUI is oriented to real AM workflow
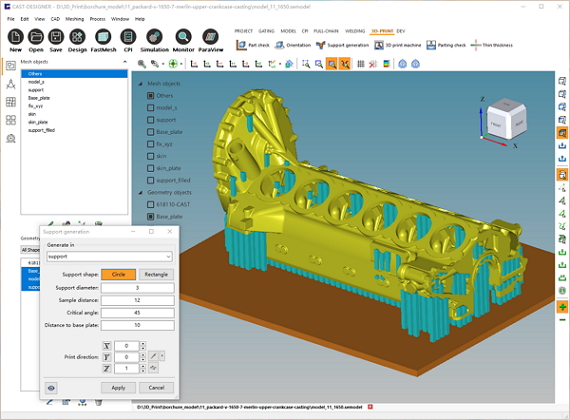
Cast-3DPrint user's interface